Dalam tahun-tahun kebelakangan ini, terima kasih kepada perkembangan pesat industri tenaga baharu, kimpalan laser telah dengan pantas menembusi keseluruhan industri tenaga baharu kerana kelebihannya yang pantas dan stabil. Antaranya, peralatan kimpalan laser menyumbang bahagian tertinggi aplikasi dalam keseluruhan industri tenaga baharu.
Kimpalan lasertelah menjadi pilihan pertama dengan cepat dalam semua lapisan masyarakat kerana kelajuannya yang pantas, kedalaman yang besar, dan ubah bentuk yang kecil. Dari kimpalan titik kepada kimpalan punggung, kimpalan binaan dan pengedap,kimpalan lasermemberikan ketepatan dan kawalan yang tiada tandingan. Ia memainkan peranan penting dalam pengeluaran dan pembuatan perindustrian, termasuk industri ketenteraan, penjagaan perubatan, aeroangkasa, alat ganti kereta 3C, kepingan logam mekanikal, tenaga baharu dan industri lain.
Berbanding dengan teknologi kimpalan lain, kimpalan laser mempunyai kelebihan dan kekurangannya yang unik.
Kelebihan:
1. Kelajuan pantas, kedalaman besar dan ubah bentuk kecil.
2. Kimpalan boleh dilakukan pada suhu biasa atau dalam keadaan khas, dan peralatan kimpalan adalah mudah. Sebagai contoh, pancaran laser tidak hanyut dalam medan elektromagnet. Laser boleh mengimpal dalam vakum, udara atau persekitaran gas tertentu, dan boleh mengimpal bahan yang melalui kaca atau lutsinar kepada pancaran laser.
3. Ia boleh mengimpal bahan refraktori seperti titanium dan kuarza, dan juga boleh mengimpal bahan yang berbeza dengan hasil yang baik.
4. Selepas laser difokuskan, ketumpatan kuasa adalah tinggi. Nisbah aspek boleh mencapai 5:1, dan boleh mencapai sehingga 10:1 apabila mengimpal peranti berkuasa tinggi.
5. Kimpalan mikro boleh dilakukan. Selepas pancaran laser difokuskan, tempat kecil boleh diperolehi dan boleh diletakkan dengan tepat. Ia boleh digunakan pada pemasangan dan kimpalan bahan kerja mikro dan kecil untuk mencapai pengeluaran besar-besaran automatik.
6. Ia boleh mengimpal kawasan yang sukar dicapai dan melakukan kimpalan jarak jauh tanpa sentuhan, dengan fleksibiliti yang hebat. Terutama dalam beberapa tahun kebelakangan ini, teknologi pemprosesan laser YAG telah menggunakan teknologi penghantaran gentian optik, yang membolehkan teknologi kimpalan laser dipromosikan dan digunakan secara lebih meluas.
7. Pancaran laser mudah dibelah dalam masa dan ruang, dan berbilang pancaran boleh diproses di beberapa lokasi secara serentak, menyediakan syarat untuk kimpalan yang lebih tepat.
Kecacatan:
1. Ketepatan pemasangan bahan kerja dikehendaki tinggi, dan kedudukan rasuk pada bahan kerja tidak boleh diseleweng dengan ketara. Ini kerana saiz bintik laser selepas memfokus adalah kecil dan jahitan kimpalan sempit, menjadikannya sukar untuk menambah bahan logam pengisi. Jika ketepatan pemasangan bahan kerja atau ketepatan kedudukan rasuk tidak memenuhi keperluan, kecacatan kimpalan terdedah kepada berlaku.
2. Kos laser dan sistem berkaitan adalah tinggi, dan pelaburan sekali sahaja adalah besar.
Kecacatan kimpalan laser biasadalam pembuatan bateri litium
1. Keliangan kimpalan
Kecacatan biasa dalamkimpalan laserialah pori-pori. Kolam cair kimpalan adalah dalam dan sempit. Semasa proses kimpalan laser, nitrogen menyerang kolam lebur dari luar. Semasa proses penyejukan dan pemejalan logam, keterlarutan nitrogen berkurangan dengan penurunan suhu. Apabila logam kolam lebur menyejuk untuk mula menghablur, , keterlarutan akan jatuh secara mendadak dan tiba-tiba. Pada masa ini, sejumlah besar gas akan mendak untuk membentuk buih. Jika kelajuan terapung gelembung kurang daripada kelajuan penghabluran logam, liang akan terhasil.
Dalam aplikasi dalam industri bateri litium, kita sering mendapati bahawa liang sangat mungkin berlaku semasa kimpalan elektrod positif, tetapi jarang berlaku semasa kimpalan elektrod negatif. Ini kerana elektrod positif diperbuat daripada aluminium dan elektrod negatif diperbuat daripada kuprum. Semasa mengimpal, cecair aluminium di permukaan telah terkondensasi sebelum gas dalaman sepenuhnya melimpah, menghalang gas daripada melimpah dan membentuk lubang besar dan kecil. Stomata kecil.
Selain punca pori yang disebutkan di atas, pori juga termasuk udara luar, lembapan, minyak permukaan, dll. Selain itu, arah dan sudut tiupan nitrogen juga akan mempengaruhi pembentukan liang.
Bagaimana untuk mengurangkan berlakunya liang kimpalan?
Pertama, sebelummengimpal, kotoran minyak dan kekotoran pada permukaan bahan yang masuk perlu dibersihkan dalam masa; dalam pengeluaran bateri litium, pemeriksaan bahan masuk adalah proses yang penting.
Kedua, aliran gas pelindung harus diselaraskan mengikut faktor seperti kelajuan kimpalan, kuasa, kedudukan, dll, dan tidak boleh terlalu besar atau terlalu kecil. Tekanan jubah pelindung hendaklah dilaraskan mengikut faktor seperti kuasa laser dan kedudukan fokus, dan hendaklah tidak terlalu tinggi atau terlalu rendah. Bentuk muncung jubah pelindung hendaklah dilaraskan mengikut bentuk, arah dan faktor-faktor lain kimpalan supaya jubah pelindung dapat menutupi kawasan kimpalan secara sekata.
Ketiga, kawal suhu, kelembapan dan habuk di udara di dalam bengkel. Suhu dan kelembapan ambien akan menjejaskan kandungan lembapan pada permukaan substrat dan gas pelindung, yang seterusnya akan menjejaskan penjanaan dan pelepasan wap air dalam kolam lebur. Jika suhu dan kelembapan ambien terlalu tinggi, akan terdapat terlalu banyak lembapan pada permukaan substrat dan gas pelindung, menghasilkan sejumlah besar wap air, mengakibatkan liang-liang. Jika suhu dan kelembapan ambien terlalu rendah, akan terdapat terlalu sedikit kelembapan pada permukaan substrat dan dalam gas pelindung, mengurangkan penjanaan wap air, dengan itu mengurangkan liang; biarkan kakitangan kualiti mengesan nilai sasaran suhu, kelembapan dan habuk di stesen kimpalan.
Keempat, kaedah ayunan rasuk digunakan untuk mengurangkan atau menghapuskan liang-liang dalam kimpalan penembusan dalam laser. Disebabkan oleh penambahan ayunan semasa mengimpal, ayunan salingan rasuk ke jahitan kimpalan menyebabkan pencairan semula sebahagian daripada jahitan kimpalan, yang memanjangkan masa kediaman logam cecair dalam kolam kimpalan. Pada masa yang sama, pesongan rasuk juga meningkatkan input haba per unit luas. Nisbah kedalaman-ke-lebar kimpalan dikurangkan, yang kondusif untuk kemunculan buih, dengan itu menghapuskan liang-liang. Sebaliknya, ayunan rasuk menyebabkan lubang kecil berayun dengan sewajarnya, yang juga boleh memberikan daya kacau untuk kolam kimpalan, meningkatkan perolakan dan kacau kolam kimpalan, dan mempunyai kesan yang baik untuk menghapuskan liang-liang.
Kelima, kekerapan nadi, kekerapan nadi merujuk kepada bilangan denyutan yang dipancarkan oleh pancaran laser setiap unit masa, yang akan menjejaskan input haba dan pengumpulan haba dalam kolam lebur, dan kemudian menjejaskan medan suhu dan medan aliran dalam cair. kolam. Sekiranya frekuensi nadi terlalu tinggi, ia akan membawa kepada input haba yang berlebihan dalam kolam lebur, menyebabkan suhu kolam lebur menjadi terlalu tinggi, menghasilkan wap logam atau unsur lain yang meruap pada suhu tinggi, mengakibatkan liang-liang. Jika frekuensi nadi terlalu rendah, ia akan membawa kepada pengumpulan haba yang tidak mencukupi dalam kolam lebur, menyebabkan suhu kolam lebur menjadi terlalu rendah, mengurangkan pembubaran dan pelepasan gas, mengakibatkan liang-liang. Secara umumnya, kekerapan nadi harus dipilih dalam julat yang munasabah berdasarkan ketebalan substrat dan kuasa laser, dan elakkan terlalu tinggi atau terlalu rendah.
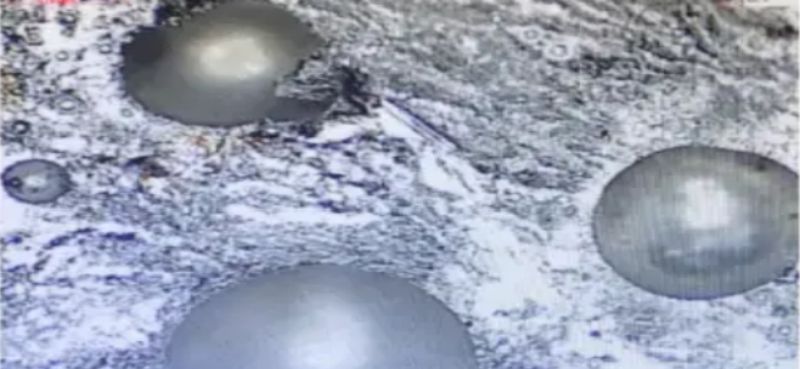
Lubang kimpalan (kimpalan laser)
2. Kimpalan percikan
Percikan yang dihasilkan semasa proses kimpalan, kimpalan laser akan menjejaskan kualiti permukaan kimpalan secara serius, dan akan mencemarkan dan merosakkan kanta. Prestasi umum adalah seperti berikut: selepas kimpalan laser selesai, banyak zarah logam muncul pada permukaan bahan atau bahan kerja dan melekat pada permukaan bahan atau bahan kerja. Prestasi yang paling intuitif ialah apabila mengimpal dalam mod galvanometer, selepas tempoh penggunaan kanta pelindung galvanometer, akan terdapat lubang padat di permukaan, dan lubang ini disebabkan oleh percikan kimpalan. Selepas masa yang lama, mudah untuk menyekat cahaya, dan akan ada masalah dengan lampu kimpalan, mengakibatkan beberapa masalah seperti kimpalan pecah dan kimpalan maya.
Apakah punca percikan?
Pertama, ketumpatan kuasa, lebih besar ketumpatan kuasa, lebih mudah untuk menghasilkan percikan, dan percikan itu berkaitan secara langsung dengan ketumpatan kuasa. Ini adalah masalah berabad-abad lamanya. Sekurang-kurangnya setakat ini, industri tidak dapat menyelesaikan masalah percikan, dan hanya boleh mengatakan bahawa ia telah dikurangkan sedikit. Dalam industri bateri litium, percikan adalah punca terbesar litar pintas bateri, tetapi ia tidak dapat menyelesaikan punca utama. Kesan percikan pada bateri hanya boleh dikurangkan dari sudut perlindungan. Contohnya, bulatan port penyingkiran habuk dan penutup pelindung ditambah di sekeliling bahagian kimpalan, dan barisan pisau udara ditambah dalam bulatan untuk mengelakkan kesan percikan atau kerosakan pada bateri. Memusnahkan alam sekitar, produk dan komponen di sekitar stesen kimpalan boleh dikatakan telah kehabisan cara.
Bagi menyelesaikan masalah percikan, hanya boleh dikatakan bahawa mengurangkan tenaga kimpalan membantu mengurangkan percikan. Mengurangkan kelajuan kimpalan juga boleh membantu jika penembusan tidak mencukupi. Tetapi dalam beberapa keperluan proses khas, ia mempunyai sedikit kesan. Ia adalah proses yang sama, mesin yang berbeza dan kumpulan bahan yang berbeza mempunyai kesan kimpalan yang sama sekali berbeza. Oleh itu, terdapat peraturan tidak bertulis dalam industri tenaga baharu, satu set parameter kimpalan untuk satu peralatan.
Kedua, jika permukaan bahan atau bahan kerja yang diproses tidak dibersihkan, kotoran minyak atau bahan pencemar juga akan menyebabkan percikan yang serius. Pada masa ini, perkara paling mudah ialah membersihkan permukaan bahan yang diproses.
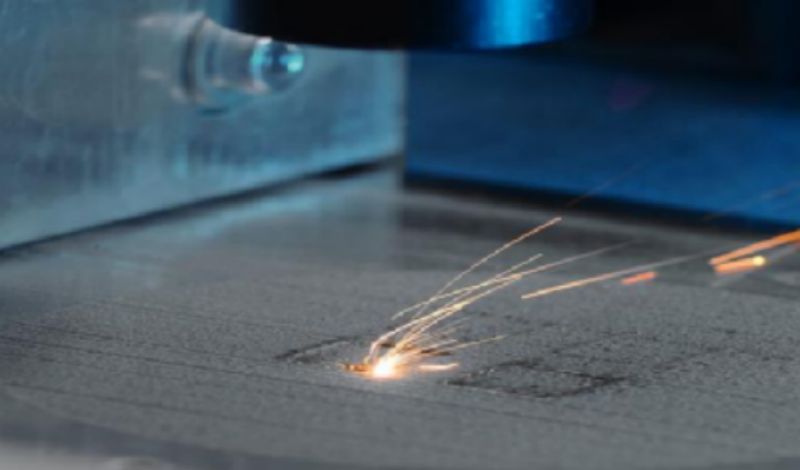
3. pemantulan tinggi kimpalan laser
Secara umumnya, pantulan tinggi merujuk kepada fakta bahawa bahan pemprosesan mempunyai kerintangan yang kecil, permukaan yang agak licin, dan kadar penyerapan yang rendah untuk laser inframerah dekat, yang membawa kepada sejumlah besar pelepasan laser, dan kerana kebanyakan laser digunakan. dalam menegak Disebabkan bahan atau sedikit kecenderungan, cahaya laser yang kembali memasuki semula kepala keluaran, malah sebahagian daripada cahaya yang kembali digandingkan ke dalam gentian pemancar tenaga, dan dihantar kembali sepanjang gentian ke bahagian dalam. daripada laser, menjadikan komponen teras di dalam laser terus berada pada suhu tinggi.
Apabila pemantulan terlalu tinggi semasa kimpalan laser, penyelesaian berikut boleh diambil:
3.1 Gunakan salutan anti pantulan atau rawat permukaan bahan: salutan permukaan bahan kimpalan dengan salutan anti pantulan boleh mengurangkan pemantulan laser dengan berkesan. Salutan ini biasanya merupakan bahan optik khas dengan pemantulan rendah yang menyerap tenaga laser dan bukannya memantulkannya kembali. Dalam sesetengah proses, seperti kimpalan pengumpul semasa, sambungan lembut, dan lain-lain, permukaan juga boleh timbul.
3.2 Laraskan sudut kimpalan: Dengan melaraskan sudut kimpalan, pancaran laser boleh berlaku pada bahan kimpalan pada sudut yang lebih sesuai dan mengurangkan kejadian pantulan. Biasanya, kejadian pancaran laser secara berserenjang dengan permukaan bahan yang akan dikimpal adalah cara yang baik untuk mengurangkan pantulan.
3.3 Menambah penyerap tambahan: Semasa proses kimpalan, sejumlah penyerap tambahan, seperti serbuk atau cecair, ditambah kepada kimpalan. Penyerap ini menyerap tenaga laser dan mengurangkan pemantulan. Penyerap yang sesuai perlu dipilih berdasarkan bahan kimpalan khusus dan senario aplikasi. Dalam industri bateri litium, ini tidak mungkin.
3.4 Gunakan gentian optik untuk menghantar laser: Jika boleh, gentian optik boleh digunakan untuk menghantar laser ke kedudukan kimpalan untuk mengurangkan pemantulan. Gentian optik boleh membimbing pancaran laser ke kawasan kimpalan untuk mengelakkan pendedahan langsung ke permukaan bahan kimpalan dan mengurangkan kejadian pantulan.
3.5 Melaraskan parameter laser: Dengan melaraskan parameter seperti kuasa laser, panjang fokus dan diameter fokus, pengagihan tenaga laser boleh dikawal dan pantulan boleh dikurangkan. Bagi sesetengah bahan reflektif, mengurangkan kuasa laser mungkin merupakan cara yang berkesan untuk mengurangkan pantulan.
3.6 Gunakan pembahagi rasuk: Pembahagi rasuk boleh membimbing sebahagian daripada tenaga laser ke dalam peranti penyerapan, dengan itu mengurangkan kejadian pantulan. Peranti pemisah rasuk biasanya terdiri daripada komponen optik dan penyerap, dan dengan memilih komponen yang sesuai dan melaraskan susun atur peranti, pemantulan yang lebih rendah boleh dicapai.
4. Kimpalan undercut
Dalam proses pembuatan bateri litium, proses manakah yang lebih berkemungkinan menyebabkan pemotongan? Mengapakah undercutting berlaku? Mari kita analisanya.
Undercut, secara amnya bahan mentah kimpalan tidak digabungkan dengan baik antara satu sama lain, jurang terlalu besar atau alur muncul, kedalaman dan lebar pada dasarnya lebih besar daripada 0.5mm, jumlah panjang lebih besar daripada 10% daripada panjang kimpalan, atau lebih besar daripada standard proses produk panjang yang diminta.
Dalam keseluruhan proses pembuatan bateri litium, pemotongan terkecil lebih berkemungkinan berlaku, dan ia biasanya diedarkan dalam pra-kimpalan pengedap dan kimpalan plat penutup silinder dan pra-kimpalan pengedap dan kimpalan plat penutup shell aluminium persegi. Sebab utama ialah plat penutup pengedap perlu bekerjasama dengan cangkerang untuk Kimpalan, proses padanan antara plat penutup pengedap dan cangkerang terdedah kepada jurang kimpalan yang berlebihan, alur, runtuh, dan lain-lain, jadi ia sangat terdedah kepada pemotongan. .
Jadi apa yang menyebabkan undercutting?
Jika kelajuan kimpalan terlalu cepat, logam cecair di belakang lubang kecil yang menghala ke tengah kimpalan tidak akan mempunyai masa untuk mengagihkan semula, mengakibatkan pemejalan dan pemotongan kecil pada kedua-dua belah kimpalan. Memandangkan keadaan di atas, kita perlu mengoptimumkan parameter kimpalan. Ringkasnya, percubaan berulang untuk mengesahkan pelbagai parameter, dan terus melakukan DOE sehingga parameter yang sesuai ditemui.
2. Jurang kimpalan yang berlebihan, alur, keruntuhan, dsb. bahan kimpalan akan mengurangkan jumlah logam cair yang mengisi celah, menjadikan pemotongan lebih berkemungkinan berlaku. Ini adalah soal peralatan dan bahan mentah. Sama ada bahan mentah kimpalan memenuhi keperluan bahan masuk proses kami, sama ada ketepatan peralatan memenuhi keperluan, dsb. Amalan biasa ialah sentiasa menyeksa dan memukul pembekal dan orang yang bertanggungjawab ke atas peralatan tersebut.
3. Jika tenaga jatuh terlalu cepat pada penghujung kimpalan laser, lubang kecil mungkin runtuh, mengakibatkan pemotongan tempatan. Padanan kuasa dan kelajuan yang betul boleh menghalang pembentukan potongan bawah. Seperti kata pepatah lama, ulangi percubaan, sahkan pelbagai parameter, dan teruskan DOE sehingga anda menemui parameter yang betul.
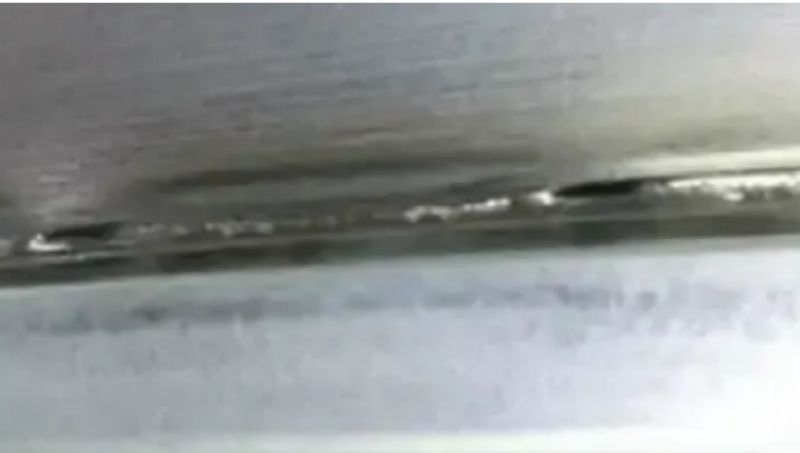
5. Pusat kimpalan runtuh
Jika kelajuan kimpalan perlahan, kolam lebur akan menjadi lebih besar dan lebih luas, meningkatkan jumlah logam cair. Ini boleh menyukarkan mengekalkan ketegangan permukaan. Apabila logam cair menjadi terlalu berat, bahagian tengah kimpalan mungkin tenggelam dan membentuk celupan dan lubang. Dalam kes ini, ketumpatan tenaga perlu dikurangkan dengan sewajarnya untuk mengelakkan keruntuhan kolam cair.
Dalam keadaan lain, jurang kimpalan hanya membentuk keruntuhan tanpa menyebabkan perforasi. Ini sudah pasti masalah kesesuaian mesin akhbar.
Pemahaman yang betul tentang kecacatan yang boleh berlaku semasa kimpalan laser dan punca-punca kecacatan yang berbeza membolehkan pendekatan yang lebih disasarkan untuk menyelesaikan sebarang masalah kimpalan yang tidak normal.
6. Kimpalan retak
Retakan yang muncul semasa kimpalan laser berterusan adalah terutamanya retak haba, seperti retak kristal dan retak pencairan. Punca utama keretakan ini adalah daya pengecutan besar yang dihasilkan oleh kimpalan sebelum ia benar-benar memejal.
Terdapat juga sebab berikut untuk keretakan dalam kimpalan laser:
1. Reka bentuk kimpalan yang tidak munasabah: Reka bentuk geometri dan saiz kimpalan yang tidak betul boleh menyebabkan kepekatan tegasan kimpalan, seterusnya menyebabkan keretakan. Penyelesaiannya adalah untuk mengoptimumkan reka bentuk kimpalan untuk mengelakkan kepekatan tegasan kimpalan. Anda boleh menggunakan kimpalan mengimbangi yang sesuai, menukar bentuk kimpalan, dsb.
2. Ketidakpadanan parameter kimpalan: Pemilihan parameter kimpalan yang tidak betul, seperti kelajuan kimpalan terlalu cepat, kuasa terlalu tinggi, dsb., boleh menyebabkan perubahan suhu tidak sekata di kawasan kimpalan, mengakibatkan tegasan kimpalan dan retak yang besar. Penyelesaiannya adalah untuk melaraskan parameter kimpalan agar sepadan dengan bahan tertentu dan keadaan kimpalan.
3. Penyediaan permukaan kimpalan yang lemah: Kegagalan membersihkan dan pra-rawat permukaan kimpalan dengan betul sebelum mengimpal, seperti mengeluarkan oksida, gris, dsb., akan menjejaskan kualiti dan kekuatan kimpalan dan mudah menyebabkan keretakan. Penyelesaiannya adalah untuk membersihkan dan pra-rawat secukupnya permukaan kimpalan untuk memastikan kekotoran dan bahan cemar di kawasan kimpalan dirawat dengan berkesan.
4. Kawalan input haba kimpalan yang tidak betul: Kawalan input haba yang lemah semasa mengimpal, seperti suhu yang berlebihan semasa mengimpal, kadar penyejukan lapisan kimpalan yang tidak betul, dsb., akan membawa kepada perubahan dalam struktur kawasan kimpalan, mengakibatkan keretakan . Penyelesaiannya adalah untuk mengawal suhu dan kadar penyejukan semasa mengimpal untuk mengelakkan terlalu panas dan penyejukan pantas.
5. Pelepasan tekanan yang tidak mencukupi: Rawatan pelepasan tekanan yang tidak mencukupi selepas kimpalan akan mengakibatkan pelepasan tekanan yang tidak mencukupi di kawasan yang dikimpal, yang akan menyebabkan keretakan dengan mudah. Penyelesaiannya adalah dengan melakukan rawatan pelepasan tekanan yang sesuai selepas kimpalan, seperti rawatan haba atau rawatan getaran (sebab utama).
Bagi proses pembuatan bateri litium, proses manakah yang lebih cenderung menyebabkan keretakan?
Secara amnya, retakan cenderung berlaku semasa pengedap kimpalan, seperti pengedap pengedap cangkerang keluli silinder atau cangkerang aluminium, pengedap pengedap cangkerang aluminium persegi, dan lain-lain. Di samping itu, semasa proses pembungkusan modul, kimpalan pengumpul semasa juga terdedah kepada retak.
Sudah tentu, kita juga boleh menggunakan wayar pengisi, pemanasan awal atau kaedah lain untuk mengurangkan atau menghapuskan keretakan ini.
Masa siaran: Sep-01-2023